PULLMAN – A Washington State University research team has received a U.S. Department of Energy award for work to recycle materials from wind turbines.
The team is one of 20 from throughout the U.S. to receive the $75,000 first-phase prize, which also makes them eligible for the second phase of the $5.1 million competition. The work is funded by the Bipartisan Infrastructure Law.
While as much as 85% of wind turbine materials can be reused, researchers are still working to effectively recycle the carbon fiber and fiberglass materials that make up the wind turbine blades, which have an average lifespan of about 20 years.
“That first generation of wind turbine blades is being retired now,” said Jinwen Zhang, a professor in the School of Mechanical and Materials Engineering who is leading the project.
The carbon fiber-reinforced materials are difficult to recycle because, unlike plastic milk bottles that can be simply melted down and reused, the composites used in wind turbine blades contain thermoset matrix resins. When they are made, they are irreversibly cured and can’t easily be undone to their original materials. In addition to wind turbines, carbon-fiber-reinforced plastics are used in many other industries, such as aviation and automotive, because they are lightweight and strong.
“It’s a growing field. They’re becoming commodities — not just specialized materials,” said graduate student Brian Bliss, “and they’re very challenging to recycle without some really clever solutions.”
In the past, researchers have mostly ground these materials down mechanically or broken them down with very high temperatures or harsh chemicals to recover the valuable carbon fiber. Oftentimes, however, the carbon fiber is damaged in the process. The caustic chemicals used are hazardous and difficult to dispose of. They also destroy the matrix resin materials in the composites, creating a messy mixture of chemicals and an additional waste problem.
Zhang and his team have been working on a new chemical recycling method that uses a mild Lewis acid as the catalyst and an eco-friendly and benign industrial solvent to break down the thermosets. The researchers are able to preserve the carbon fibers as well as the resin material in a useful form that can be easily re-used. Their formula works at moderate temperatures below 200 degrees C and ambient pressure without the need for a pressure chamber.
“A pressure chamber would add additional costs in operation as well as in capital investment,” said Zhang. “For our system, a high boiling point organic solvent is perfect, and people are used to it in industry.”
After shredding the material into chips, the researchers can break down the carbon fiber material in three hours and still preserve the strength properties of the original carbon fiber.
Baoming Zhao, a staff scientist in the group, calls this reaction medium a “magic solvent” with unique chemical properties that provides excellent separation abilities.
Their process can also be done in a continuous or semi continuous process without generating any secondary waste, he added. The solvent runs through the waste material and dissolves the matrix resin, which can then be collected using water precipitation.
“Then we can bring that solvent back, and since it has that really good temperature, and long-term stability, we can recover it and reuse it for the next batch of recycling,” said Bliss. “That means that as we scale up, we can reduce costs in the process.”
As part of the award, the researchers will be working to optimize their process, scale it up, and demonstrate the semi-batch process.
“Our process is novel, creative, and unique because this is the first time we can do the recycling in a continuous process and under a moderate temperature,” said Zhang. “That’s a huge benefit for recycling. The continuous chemical recycling process hasn’t been seen anywhere else.”
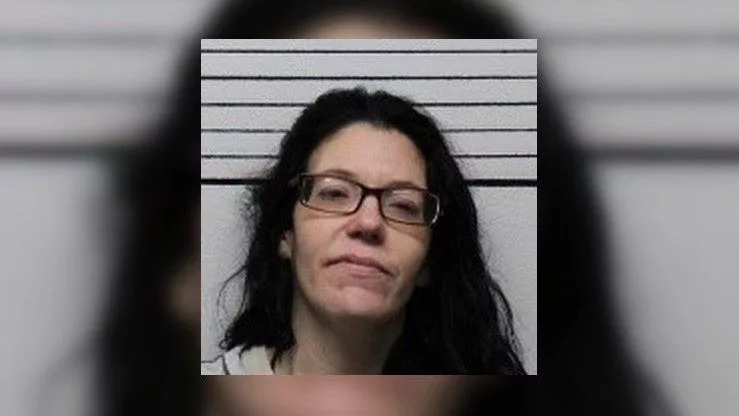